Takt Time
Le Takt Time est le rythme auquel les produits ou services doivent être produits pour répondre au rythme de la demande des clients. Il est dérivé du mot allemand, Taktzeit, qui est souvent désigné comme le battement de cœur ou le battement de tambour de la production dans le Lean Manufacturing.
Cette valeur, en conjonction avec les taux de chargement (production) actuels, est utilisée pour analyser les charges de processus, les goulots d’étranglement et la capacité excédentaire. L’étude indiquera quelles opérations sont en avance sur le taux de demande et lesquelles ne le sont pas, les deux indiquant des possibilités d’amélioration. Il s’agit strictement d’une formule et d’un calcul. Utilisez-la pour comparer le » chargement » mesuré afin de quantifier si une opération atteint ou dépasse le takt time et de combien.

L’unité de temps dans le numérateur & dénominateur doit être la même.
Le numérateur, le temps de travail disponible, est souvent exprimé en minutes/poste, secondes/jour, minutes/jour et ainsi de suite.
Le dénominateur, le taux de demande du client, est souvent exprimé en pièces/minute, unités/équipe, pièces/jour, et ainsi de suite.
EXEMPLE:
Le premier processus est étiqueté PROCESSUS 1 car si la quantité de temps de travail disponible OU la demande sur cette machine particulière ou ce groupe de machines varie d’un processus à l’autre, alors chaque processus aura son propre takt time.
|
Un calculateur de temps de Takt (ainsi que d’autres modèles et calculateurs) avec un exemple est disponible ici. Les formules au sein de la feuille de calcul sont visibles pour aider à comprendre l’impact des entrées. |
Les valeurs de temps Takt sont rarement les mêmes sur l’ensemble du flux de valeur si l’aménagement est départementalisé. Il y a de fortes chances que ces machines (processus ou services) partagent la demande. Cependant, dans de nombreuses cellules de travail, toutes les machines ont le même taux de demande du client et le même temps de travail disponible, ce qui rend l’activité d’équilibrage de ligne plus facile.
Exemple :
Si le client A commande 55 000 unités/jour qui nécessitent le processus 1 (du haut) et que ces unités nécessitent également le processus 2 en aval
ET
Le client B passe maintenant une commande et veut 55 000 unités/jour qui nécessitent le processus 1 mais PAS le processus 2…..alors le takt time de chaque processus est différent.
Sachant que le travail disponible est le même pour chaque processus à 22 heures/jour = 1 320 minutes par jour = 79 200 sec/jour.
CALCUL :
Processus 1 : Takt Time= 79 200 sec/jour / 110 000 unités/jour = 0,72 seconde / unité
Processus 2 : Takt Time = 79 200 sec/jour / 55 000 unités/jour = 1,44 seconde / unité
Conclusion
Le taux de charge (taux de production) doit être deux fois plus rapide sur le processus 1 que sur le processus 2 pour suivre la demande des clients.
Les opérations dont les performances sont supérieures au takt time ont également des possibilités d’amélioration ; souvent, la charge d’un processus en retard peut être déchargée et partagée. La quantité est déterminée par les différences dans les études de la charge actuelle et du takt time pour chaque processus.
Le nivellement de la charge de travail, l’équilibrage des lignes, à travers les processus en étudiant ces valeurs est le travail de l’équipe.
L’étude est normalement représentée à l’aide de graphiques à barres et ne montrera pas seulement les goulots d’étranglement ou la capacité excédentaire, mais quantifiera également la quantité et la relativité entre toutes les opérations.
Interpréter le graphique
Le graphique ci-dessous montre les résultats d’une évaluation des neuf processus (A-H) pour produire un produit particulier.
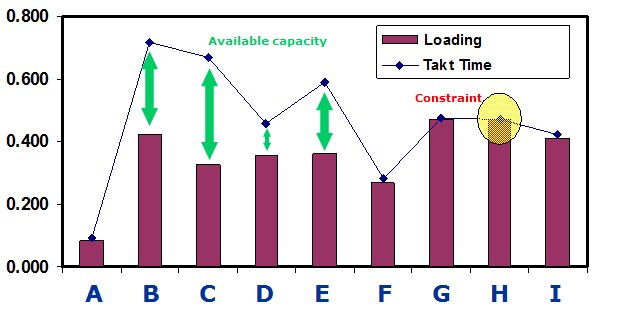
Quels sont les points à retenir ?
- Les processus B, C, D, E ont une capacité excédentaire puisqu’ils dépassent la demande du client ou takt time. Dans une telle situation, évaluez la main-d’œuvre pour la possibilité de la déplacer vers une opération de contrainte ou de réduire les heures supplémentaires.
- Les processus A, F, G, H et I sont presque parfaitement appariés et performants au takt time. En réalité, cela est très difficile à réaliser et à maintenir la charge au niveau exact du temps de takt. D’une part, le takt time change souvent (la demande des clients change).
- Le processus H peut être une contrainte mineure. Peut-être qu’un événement SMED pourrait apporter suffisamment d’améliorations pour atténuer tout goulot d’étranglement.
Dans ce type de situation, il ne devrait pas y avoir de retard de livraison au client. Bien sûr, il s’agit d’un instantané dans le temps. Si le chargement ou le takt time ont beaucoup de volatilité (ou de variation), alors cela n’apparaîtra pas forcément dans ce graphique. Comme avec tout outil qui représente un instantané dans le temps, la variation pourrait entraîner de nombreux problèmes.
Goulots d’étranglement
Les opérations à goulots d’étranglement sont celles pour lesquelles le cycle de charge > Takt Time.
Les membres de l’équipe savent probablement déjà quelles opérations ont une capacité et quelles sont les contraintes, mais ce qu’ils ne savent pas, c’est l’étendue ou le degré et la quantité par rapport aux autres processus.
Pour répondre aux demandes de livraison du client, chaque goulot d’étranglement devra être résolu de façon à ce que le chargement soit plus rapide que le takt time.
Mais où faut-il concentrer ses efforts en premier lieu ?
L’étude ne fournira que des chiffres. Une petite contrainte dans un domaine en raison d’un taux de rebut et de reprise élevé peut être beaucoup plus coûteuse globalement qu’une contrainte de temps plus importante dans un autre domaine.
Ces chiffres ainsi que le raisonnement sur les coûts, les rebuts et d’autres mesures subjectives sont destinés à l’équipe pour déterminer la priorisation des améliorations.
C’est pourquoi un professionnel des finances et les principales parties prenantes doivent contribuer à l’équipe. En tant que gestionnaire de projet Six Sigma, vous pouvez seulement présenter les chiffres, mais aussi offrir ce qui n’est PAS dans les chiffres et qui pourrait changer les priorités.
Le but est d’obtenir l’équilibre de toute la ligne tout en éliminant les déchets. La réduction des déchets (reprise, rebuts, surproduction et autres 7 déchets) doit être ciblée de manière agressive, puis une étude de chargement doit être réalisée avant d’investir de manière significative dans l’équilibrage de la ligne.
Vidéos & Plus d’exemples
Retour à la phase IMPROVE
Retour à LEAN MANUFACTURING
S’abonner pour accéder à l’ensemble du site
Modèles, tableaux, et calculateurs
Retour à la page d’accueil du matériel Six-Sigma-Material Home Page
Articles récents
- .
-
-
-
Distribution t, test t
Mar 11, 21 10 :56 AM
Exploration de la distribution t et du test t, test t à 1 échantillon, test t à 2 échantillons
-
Matériel Six Sigma, formation, cours, calculatrices, certification.
Jan 29, 21 11:01 AM
Un site avec le matériel Six Sigma le plus courant, des vidéos, des exemples, des calculatrices, des cours et une certification.
-
Certification Six Sigma, certification Ceinture verte et Ceinture noire
Jan 06, 21 08:32 AM
Décrit les types de certification Six Sigma comme Ceinture verte, Ceinture noire et Master Black Belt
.